モノづくり座談会
スマートな加工工程の確立に向け
3DAモデルの活用と、ノウハウを活かす工程設計 【日本物流新聞/2024年5月25日号より転載】
デジタルエンジニアリング、フロントローディング(※1)といった言葉が製造業の間で使われるようになって四半世紀以上。設計サイドの意思を下流までデジタルで一気通貫させようという試みはしかし、DXが叫ばれる今も課題解決、普及ともに「まだ道半ば」の印象が免れない。
そこで座談会を開催し、モノづくりの全域でデジタルを活かすスマートな工程を確立するために必要なことを、この分野の研究実践と知見で知られる竹内氏(中部大学理事長・学長)に加わっていただき、設計・製造・測定のそれぞれに関係する生産財メーカーの技術幹部にあらためて考えてもらった。座談会出席者はいずれも、デジタルエンジニアリングに絡む経済産業省の調査プロジェクトに日本工作機械工業会のメンバーとして参加しており、「語る」だけでなく「実践」を視野に入れている。先に結論めいたことを書けば、3D化でカバーできる領域の整備と、差別化を生む競争領域を分けながら「日本発の先端モノづくりを目指すべき」との流れになった。
※1)フロントローディング…加工の上流(フロント)に負荷をかけ(ローディング)、工程の初期段階で作り込むプロセスを指す。概念は以前からあったが、バーチャル検証やデジタルツインの活用などで高度な実践が期待される。
02 人が作る工程設計の重要性―自動化できないものは残る
一気通貫をある種の理想として追い求めながらも、モノづくり工程での競争要因は、ひとつに「人が作る工程設計だろう」との指摘が話の中で何度か出た。このあたりの重要性を慎重に確認しながら、産学連携による研究開発の在り方にも話題を広げた。
出席者
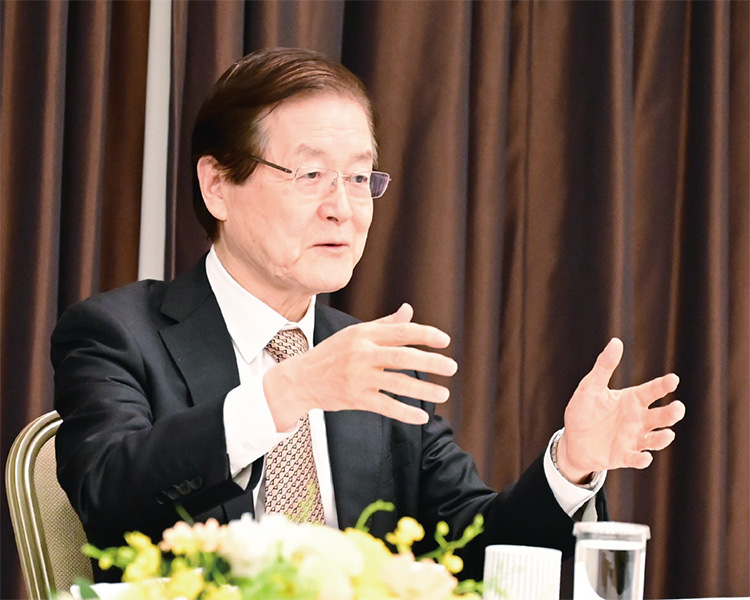
理事長・学長
竹内 芳美 氏
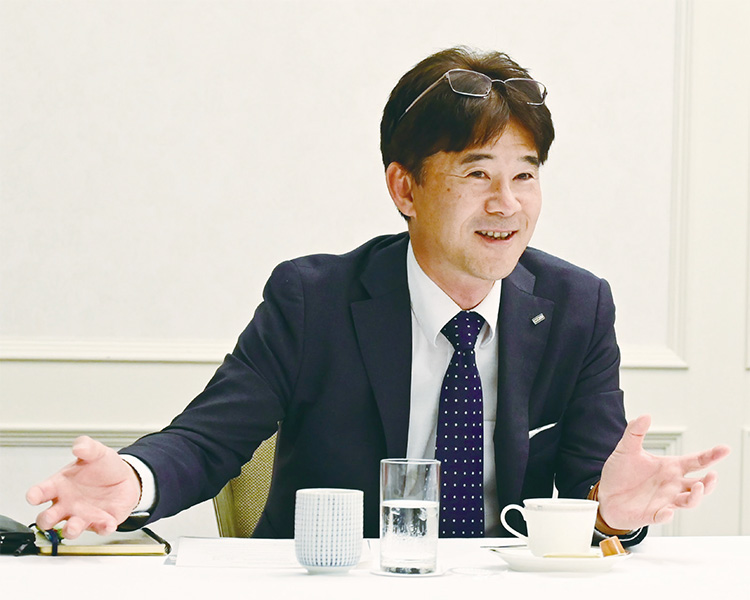
執行役員商品企画統括部長
小泉 哲 氏
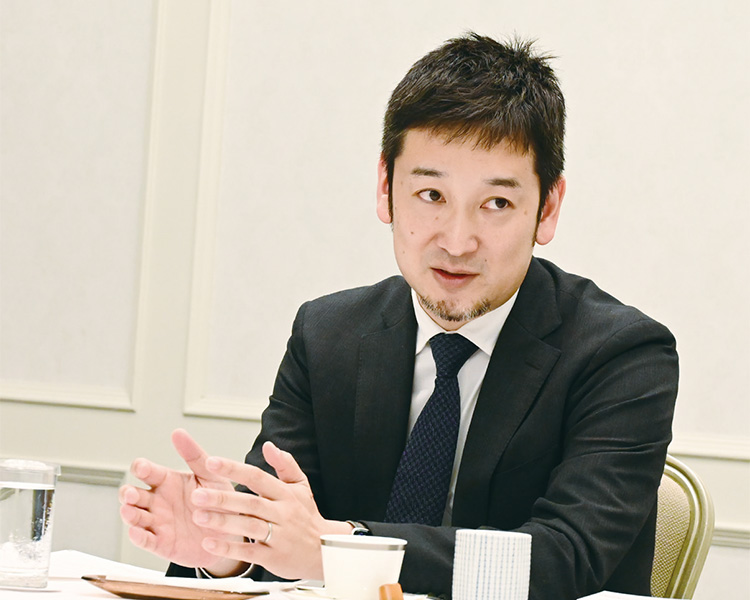
執行役員開発本部副本部長
藤田 祥 氏
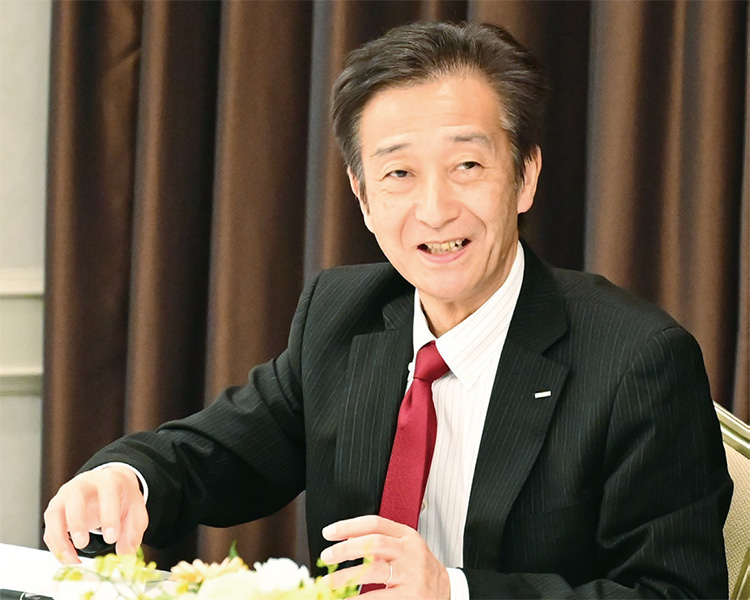
フェロー
阿部 誠 氏
小泉 もう一度整理しておきたいのですが、ここでの話は一品物とか、また私どもが大変お世話になっている金型業のモノづくりとは違う、量産型のモノづくりを対象にして、その全工程をデジタルでカバーしつつ、人の技術やノウハウも活かすという話ですよね。
阿部 そういうことです。一定程度の量を持つ加工において、今後どういうプロセスを作り上げていくか。恐らく試作段階からしっかり決めていくべきことでしょうが、ようは従来のフロントローディングを進めるだけでいいのかということを考えたいと思います。もっとも、金型で作る素材・部品、鋳鍛造品の調達なども含めて全体で進めるべきことですが。
小泉 なるほど。金型加工のことを少し言いますと、1次加工の公差のアウトプット、続く2次加工のインプットとアウトプットという流れは当然意識して出力するわけです。CADCAMでできることは、手元にあるデータベースを特性に応じて割り当てるということです。
本紙 CGSさんはAIを使ったパスの最適化などもツールとしてリリースされましたね。
小泉 いや最適化というか、私どもが始めたのは、工具が持っている諸条件と、材料側の諸条件を掛け合わせて、例えば工具メーカーさんが公開されていない材料を使う場合でも基準となる切削条件を導出する機能を作ったということです。この機能は最終ユーザーに活かしてもらいたいけど、この座談会で出ている中間工程でどこまで精度を追い込むか、あるいはどういう工程を組むかというところまではCADCAMは担っていません。
本紙 そこもデジタル、AIでやろうとの試みはあるんでしょうか。
阿部 ある大手製造業さんがデジタルを使って工程設計の自動化を試行されたが、効果が出ずにやめられたという話は間接的に聞いています。デジタル化を進めつつも、デジタルだけには頼れない大事な部分は確かにあります。
本紙 その大事な部分が競争領域ということなのでしょうね。工程設計は現場の人間の力、個々の組織の力で作っていくと。
藤田 工程設計の担い手は私どもからみたユーザーさんで、機械やソフトメーカーが直接関与するということでは基本ないですね。当社の工作機械をツールとして提供するか、システムで提供するかで当然変わってはきますが、基本的に与えられたインプットを削りで再現することが私たちの役目ですから。
小泉 同感ですね。CAMメーカーも図面通りにモノができるようにパスを出すことが仕事です。しかしユーザーさんは他の素材や部品と組み合わせた時の累積誤差といったことも注意深く見ながら工程をチェックされる。そこは機械やソフトメーカーが入り込む領域では基本無いでしょう。
本紙 その部分での研究や取り組みは進んでいるのでしょうか。
阿部 私の感覚で言わせていただくと、工程のデジタル化はオープン(標準化)を指向した研究として進んできたけれど、デジタルに絡む最近の産学連携などをみると、工程設計の在り方なども含めむしろクローズドな研究が増えているように思います。
本紙 竹内先生、産学連携の研究はいまどんな感じでしょう。
竹内 どこそこの会社や企業と共同研究するといった申請は、学内で頻繁に上がっていて、以前は産学連携の必要性が取り沙汰されましたが、今はもう日常になったと言えます。
藤田 ユーザーさんからは大学教授の協力を得て取り組んでいる、つい最近も当社に来てもらったといった話をよく耳にするようになりましたね。
本紙 そうした動きの中で、オープン・クローズドの両面で成果が増えればと思います。
阿部 ええ。話は飛びますが、ドイツでは有力大学の工学部教授が政府機関の研究所所長を兼ねているケースも少なくなく、学・官の研究が民間に降りてきやすい形になっていますよ。
竹内 そう。少し前の話ですが、ドイツのアーヘン工科大学の教授が別の研究所の技術部門トップを兼任し、その研究所では部門ごとに200人からの優秀な研究所員がいるという形でした。おそらく今もそうでしょう。研究所には教授を頂点にしたヒエラルキーが3つ、4つとあって組織としてしっかり動いている。そうしたなかで大学や、大学と関係の深い研究所に開発を委託し、自分たちでは開発部隊をほとんど持たないメーカーもドイツには多いですよ。(資金も研究者の数も日本とはケタ違いですよね、の声)
藤田 教授が民間企業の社長になったり、企業の技術トップが教授になったりということも日本と比べて多いと思います。
竹内 そうした産学、あるいは産学官の連携の強さが、人口で日本の3分の2ほどのドイツが、昨年GDP実額で日本を上回った理由の一つにあるんじゃないかと率直に感じます。国際規格づくりも非常に上手いですし。
本紙 クローズドな研究で個別企業を支援し、他方でオープンなスタンダード化でもリードしている?
阿部 ええ。クローズドな取り組みの中身はなかなか見えてきませんが、ドイツでの産学連携が個々の企業の競争力や生産性に貢献していることは確かでしょう。私自身、長年ドイツの隣国のオランダに赴任していましたが、従業員は残業なんかまず絶対しないし、毎年4週間超の長期休暇も取っていた。強さの背景には効率のいい仕組みづくりがあって、見習うところは大いにあると思います。
関連商品 カタログダウンロード
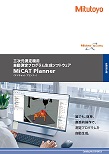